Background
As a college chemistry student I was eager to read the labels on every product I could find to bask in my newfound knowledge of organic nomenclature. Imagine my frustration when I found more useful information on a bottle of shampoo than I found on a can of Lacquer Thinner. Fortunately, labelling has improved, and most major components can be found on the sides of the can.
Still, I suffered with the lingering question of “Why did they mix toluene and MEK to make product X?”. It was an exciting day in 2006, when a student came into the office and asked me why I wasn’t using the Hansen Solubility Parameters to pick solvents. I had sent her on a literature search for solubility models, and she found the Hansen Solubility Parameters Handbook 1st Edition. (Don’t be too hard on me. I was raised as a vibrational spectroscopist and had little experience in solubility studies.) A quick view of the book gave me a “Eureka” moment, as I found ways to blend solvents, and “stick non-stick surfaces to a surface”.
I have been modelling solvent blends for recrystallization, precision cleaning, and polymer swelling for about 3 years. Much of my initial work was in an Excel spreadsheet using the equations in the CRC Handbook on the Hansen Solubility Parameters. But I eventually “graduated” to using the HSPiP software and eBook1 available at http://www.hansen-solubility.com/.
Glove Selection
Perhaps your lab is typical in selecting nitrile gloves for everything. Changes are made when one loses a finger (of a glove) in a beaker of solvent. This is not the best practice, but many will not believe me when I say that there is an “easy alternative” to the “lost-finger” selection scheme.
Of course, a chemical compatibility guide is an easy alternative. The table below is an example from North Safety.
Table 1: Chemical compatibility chart for selecting hand protection. The evaluations depend upon degradation (D), breakthrough time (BT), and permeation rate (PR). Both references explain these in detail, but the color code is obvious – green is good.
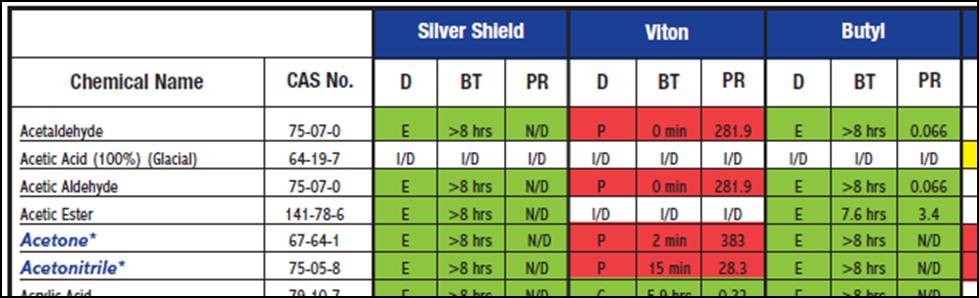
It is a pain if your solvent is not listed in the chemical compatibility table. What if you want to buy one glove that gives the best protection across a large group of solvents? What do you do if you are working with a solvent blend?
The following table from the Hansen Solubility Parameter eBook (Chapter 16) gives the HSP information for eight different glove materials.1 (If you are not familiar with the HSP theory, then see the HSPiP site http://www.hansen-solubility.com/index.php or the Wikipedia page http://en.wikipedia.org/wiki/Hansen_solubility_parameter.
Table 2: The HSPs of various glove materials computed using various solvent breakthrough times. The glove materials are nitrile (NR), butyl rubber (BR), natural rubber/latex (NAT), polyvinyl chloride (PVC), polyvinyl alcohol (PVA), polyethylene (PE), Viton (VIT), and neoprene (NEO) | ||||
Glove Type – Breakthrough | δD | δP | δH | R |
NR 20 MIN (58 to 178) | 17.5 | 7.3 | 6.5 | 5.1 |
NR 1 HR (61 to 178) | 16.6 | 9.1 | 4.4 | 10 |
NR 4 HR (58 to 178) | 19 | 12.6 | 3.8 | 13.3 |
BR 20 MIN (71 to 110) | 16.5 | 1 | 5.1 | 5 |
BR 1 HR (71 to 126) | 15.8 | -2.1 | 4 | 8.2 |
BR 4 HR (All from 71) | 17.6 | 2.1 | 2.1 | 7 |
NAT 20 MIN (61 to 267) | 14.5 | 7.3 | 4.5 | 11 |
NAT 1 HR (56 to 325) | 15.6 | 3.4 | 9.1 | 14 |
NAT 4 HR (up to 325) | 19.4 | 13.2 | 7.7 | 19 |
PVC 20 MIN (61 to 267) | 16.1 | 7.1 | 5.9 | 9.3 |
PVC 1 HR (61 to 267) | 14.9 | 11.1 | 3.8 | 13.2 |
PVC 4 HR (up to 149) | 24.4 | 4.9 | 9.9 | 22.7 |
PVA 20 MIN (All) | 11.2 | 12.4 | 13 | 12.1 |
PVA 1 HR (All) | 15.3 | 13.2 | 13.5 | 8.8 |
PVA 4 HR (All) | 17.2 | 13.6 | 15.4 | 10.9 |
PE 20 MIN (All from 40) | 16.9 | 3.3 | 4.1 | 8.1 |
PE 1 HR (All from 40) | 17.1 | 3.1 | 5.2 | 8.2 |
PE 4 HR (All from 56) | 24.1 | 14.9 | 0.3 | 24.3 |
VIT 20 MIN (All) | 10.9 | 14.5 | 3.1 | 14.1 |
VIT 1 HR (56 to 178) | 16.5 | 8.1 | 8.3 | 6.6 |
VIT 4 HR (All to 178) | 13.6 | 15.4 | 8.6 | 14.4 |
NEO 20 MIN (75 to 178) | 17.6 | 2.5 | 5.9 | 6.2 |
NEO 1 HR (69 to 178) | 19 | 8 | 0 | 13.2 |
NEO 4 HR (61 to 266) | 14.6 | 13.9 | 2.3 | 15.9 |
Table 2 gives you information about the gloves. A table of HSPs for the solvents is all you need to find the glove compatibility. The HSPiP software contains the HSPs for over 10,000 solvents and substances.
Example – A non-flammable grease remover
The 3M Novec HFE-7100 is a non-flammable, non-ozone-depleting solvent, but its solvency or solvent power is not very strong (low δT). It can be blended into flammable solvents to reduce their flammability. (Don’t try this at home, kids. It is very volatile, and will leave the blend if given the chance. The result is your “non-flammable” blend is flammable again. Of course, high-boiling azeotropes of HFE-7100 would be grand; but that is a different topic.)
We have determined the HSPs for Dow Corning High Vacuum Grease, and the following blend is a good non-flammable solution for removing this grease (41% cyclohexane, 39% ethyl acetate, and 20% HFE-7100). What glove should we select for a grease removal process that uses this blend?
The compatibility chart is no help in this case. The cyclohexane component is compatible with the Silver Shield, Viton, and Chemsoft products. The ethyl acetate component is compatible with the Silver Shield and Butyl products. The HFE-7100 component is not evaluated on this compatibility chart. Do we simply go with the Silver Shield glove since it hits 2 out of 3 components? Well, those gloves are $14 a pair from VWR!
The “better way” I mentioned earlier uses the relative energy difference (RED). Refer to the glove material table above. It has a column labelled R which is the interaction radius of the polymer. These gloves interact significantly with solvents whose HSPs are within this radius. The RED is the distance of the solvent or blend divided by the polymeric material radius. A large RED means minimal interaction. The conditional formatting tool in Excel 2007 can be used to give a very nice visual result (Figure 1). For pure cyclohexane, the polyvinyl alcohol gloves would be the best choice, and the nitrile gloves would work for short exposure or double-gloved splash protection.

Figure 1 The RED scoring of the glove materials against cyclohexane (RED #1). Green indicates better chemical resistance.
The second component of the blend is shown in Figure 2. Polyvinyl alcohol is the best choice for this solvent, too. Nitrile is NOT a good choice, but butyl rubber would work as a secondary choice if working with pure ethyl acetate. If this were a binary blend, one could safely use PVA gloves.

Figure 2 The RED scoring of the glove materials against cyclohexane (RED #1), and ethylacetate (RED #2). Green indicates better chemical resistance.
The third component of the blend is shown in Figure 3. PVA is a good choice for this component, also. But when working with blends, it is necessary to actually check the HSPs of the blend. These are computed as a volume-fraction-weighted sum of the δD, δP, and δH values of the blend components. For example, the δD for the blend is 15.8 MPa1/2, which was computed by 41%(16.8) + 39%(15.8) + 20%(13.7).

Figure 3 The RED scoring of the glove materials against cyclohexane (RED #1), ethyl acetate (RED #2), and HFE-7100 (RED #3). Green indicates better chemical resistance.
The RED score is shown for the blend in Figure 4. The PVA glove is the best choice in this case. Notice that the nitrile glove material is predicted to be somewhat resistant to the blend, but Viton would be a better backup glove material.

Figure 4 The RED scoring of the glove materials against cyclohexane (RED #1), ethyl acetate (RED #2), HFE-7100 (RED #3) and the blend. Green indicates better chemical resistance.
Conclusions
The HSP approach for glove selection is flexible. One could buy polyvinyl alcohol gloves for this operation. However, it appears that the selection of PVA gloves is limited to PVA on a support layer. This increases the cost to over $50 / pair (VWR/Ansell Healthcare). The extra cost is offset, though, because support coated gloves are much more durable and can be re-used.
A second option would be to double-glove with a nitrile glove inside a Viton glove if those were readily available in the laboratory. But Viton gloves are not inexpensive, either, at $110 / pair (VWR/Best Glove). These Viton gloves are unsupported and may be less durable than the PVA coated gloves.
The $14-a-pair Silver Shield gloves are not looking so bad when compared to Viton or PVA glove costs. But what about Silver Shield’s resistance to HFE-7100? The description of the Silver Shield product on the VWR website is:
Gloves feature a five-layer fabric compacted to a thickness of 2.7mil. Laminating a high-energy polymer (EVOH) with a low-energy polymer (PE) creates a fabric impervious to at least 90% of all organic chemicals for four hours at 35°C.3
The Silver Shield glove would be a good choice, but for added assurance, a nitrile inner glove could be added to assure resistance to HFE-7100 breakthrough.
A fourth approach would be to double glove with nitrile gloves, and keep the operation short. At 42 cents per glove, one could change gloves every hour. An eight-hour shift of degreasing would use a maximum of 32 gloves (2 hands x 2 gloves x 8 hours) giving a cost of $13.44 per shift. This is a conservative estimate of cost because I have yet to see any shift produce 8 actual hours of operations.
Finally, these conclusions are based upon the data in Figure 4, and considerable time was saved by not having to consider using butyl rubber, latex, PVC, polyethylene, or neoprene gloves. This approach gives confidence that the glove selection options are knowledge-based, and not just a roll-of-the-dice to fill in the gaps of a compatibility chart.
References
- Abbott, S.; Hansen, C. M.; Yamamoto, H.; and Valpey III, R. S. Hansen Solubility Parameters in Practice, 3rd Ed. [Online]; Publisher: Hansen-Solubility.com; 93-94. http://www.hansen-solubility.com/index.php (accessed January 5, 2011).
- Chemical Chart for Hand Protection, North Safety Products, North by Honeywell, 2000 Plainfield Pike, Cranston, RI 02921, 800-430-4110, honeywellsafetyproducts@honeywell.com, http://www.northsafety.com (accessed January 5, 2011)
- Silver Shield*/4H* Gloves, North Safety Products, https://www.vwrsp.com/catalog/product/index.cgi?catalog_number=11000-650&inE=1&highlight=11000-650 (accessed January 7, 2011)
PDF Version of this post (2011-BlogPost_HSP_Glove_Selection)
Revision History
- Original Post: 01/06/2011
- Revised: 01/07/2011 – Added cost benefit analysis to the Conclusions Section.
About the Author: Dr. Darren L. Williams is an Associate Professor of Physical Chemistry at Sam Houston State University. When he is not blending solvents, he is tinkering with contact angle measurements, FTIR microspectroscopy, etc. http://www.shsu.edu/~chm_dlw/ . He welcomes your comments and questions by phone (936-294-1529) and by email (williams “at” shsu “dot” edu)